The U.S. Energy Information Administration (EIA) reported that hydropower was responsible for 6.2% of the United States' total electricity production and approximately 28.7% of the total for renewable energy generation in 2022. Renewables provide about 20% of the country’s electricity, and this number is projected to increase over the next few years.
This article covers the basics of hydropower, explaining how it is generated and the role of penstocks – one of the most important components of hydropower systems. It also discusses how modern nondestructive testing technologies can help ensure these critical structures operate efficiently and reliably as the demand for renewable energy grows.
Hydropower Energy Basics
Half of the United States’ hydropower production is concentrated in the West, with about 50% of power generation coming from Washington, California, and Oregon. Namely, Washington is home to the Grand Coulee Dam, the largest hydropower facility in the U.S. which provides 6,800 MW of generating capacity, representing 8.5% of the country's 80,000 MW of hydropower capacity.
Across the country, hydropower usage varies significantly. Delaware and Mississippi are the only states that do not consume any hydroelectric power. In contrast, hydroelectric power accounts for 67% of Washington state’s power usage.
How Does Hydropower Work?
Hydroelectric power generation uses the flow of water to spin a turbine which activates a generator that converts the kinetic energy into electricity. There are three types of hydropower facilities: impoundment, diversion, and pumped storage. They range in size and capacity, from powering single homes to providing electricity for utility companies.
Impoundment Facility:
Impoundment facilities are the most common. Majority are large hydropower systems with capacities exceeding 30 MW. In this configuration, dams are used to accumulate water in a reservoir. When water is released, it flows through a penstock before turning the turbine.
The flow of water can be adjusted to meet energy, recreational, or environmental needs. The 2,080 MW Hoover Dam in Nevada is a well-known example of an impoundment hydro facility.
Diversion Facility:
As the name suggests, these plants divert flowing river water through a penstock and/or canal to a powerhouse at a lower elevation. They often have little or no water storage, and power generation is hinged on the river flow.
Because of this, they are typically less reliable than impoundment facilities as a consistent source of energy. An example of a major diversion system is the Chief Joseph Dam near Bridgeport, Washington which has a capacity of over 2,000 MW.
Pumped Storage Facility:
These facilities are often compared to batteries. In times of low power demand, they store energy by pumping water through a penstock from a lower reservoir to a higher reservoir. In times of high demand, the water is released back into the lower reservoir, which pushes the turbine to generate power.
The most notable pumped storage facility is the Bath County Pumped Storage Station in Bath County, Virginia with a net generating capacity of 3,000 MW. The Bath County station is the second largest pumped storage facility in the world and accounts for 13% of the United States’ pumped storage capacity.
What is a Penstock?
The penstock is one of the important components in the functioning of a hydropower system. Penstocks are pressure vessels in the form of a channel or pipe that carries water from the source to the turbine in the power station.
Depending on the size of the facility, they vary in length, circumference, and number. For example, the Hoover Dam has two sizes of penstocks. One set is 30 feet (9 meters) in diameter, and the dam also uses sixteen 13 foot (4 meters) diameter penstocks that total 5,800 feet (1,770 meters) in length. Whereas, the Bath Creek Pumped Storage Station contains three penstocks that are 28.5 feet (8.7 meters) in diameter along each 3,780 foot (1,152 meters) long penstock.
-1.jpeg)
Most penstocks are constructed from steel and may be buried underground, situated above ground with steel or concrete saddle supports along the length of piping, or encapsulated inside concrete towers or tunnels (shown above). The metal vessels carry water, making them prone to corrosion mechanisms, including uniform corrosion, crevice corrosion, pitting, and erosion corrosion.
- Uniform corrosion: the most common form of corrosion, it is the attack of a corrosive environment on the metal surface at a uniform rate
- Crevice corrosion: the attack of the metal surface by stagnant water in crevices and under coatings; for example, at expansion joint and pipe supports
- Pitting: localized corrosion that produced holes or cavities in an otherwise resistant surface
- Erosion corrosion: the combined effect of erosion and corrosion caused by the flow of turbulent water on the metal surface
In the United States, hydropower facilities have been in operation for an average of 69 years. According to EIA records, the 50 oldest power plants in the country are all hydroelectric, some dating back to the late 1800s. That being said, it’s essential that these large pieces of equipment are regularly inspected to develop preventative maintenance plans.
The Federal Energy Regulatory Commission (FERC) recommends that penstock shells should be visually inspected once a year to look for leaks, misalignment, missing rivets, and other damage. However, this may not always be possible for penstocks that are buried underground. Additionally, penstocks should be inspected with ultrasonic testing (UT) methods at a minimum of every five years to check for shell thinning due to corrosion and erosion.
For buried or encapsulated penstocks, a UT inspection can be performed internally by dewatering, or removing the water from the equipment. For penstocks that aren't able to be dewatered, remotely operated vehicles or robots may be used to collect visual and UT data.
However, these techniques are generally less effective than other internal inspection methods. When dewatering is possible, internal visual and UT inspections are the preferred methods for identifying damage from erosion, corrosion, pitting, and organic growth.
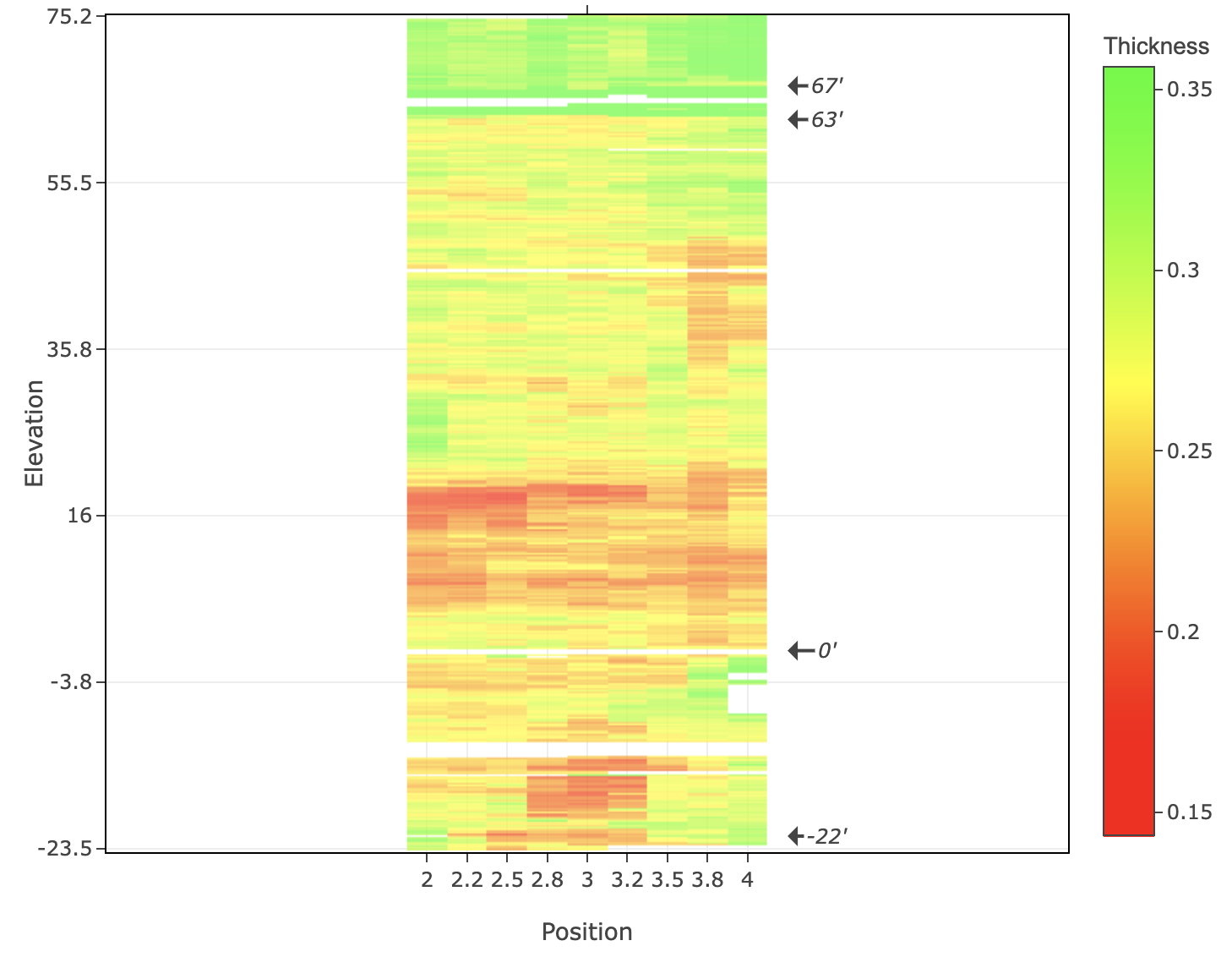
Traditionally, UT readings are taken manually at select locations along the penstock. However, this method only produces a limited data set about the condition of a large piece of equipment. As hydropower facilities age, a more holistic picture of asset health is needed to prevent failures that can lead to flooding, environmental degradation, and even loss of life.
Fortunately, modern robotic techniques allow for full asset coverage at unprecedented efficiency and data density. Rapid Ultrasonic Gridding (RUG) is a robotic UT technique for generalized corrosion mapping, depicted above. Rapid Automated Ultrasonic Testing (R-AUT) utilizes a dual linear phased array probe to identify and quantify wall thinning due to corrosion and pitting in the base metal of equipment. This is a high-definition version of corrosion mapping. Additionally, robot-enabled Rapid Auto Weld (RAW) inspection is used along the weld lines, collecting an immense amount of data to detect corrosion, cracking, and other defects.
Ensure Reliable Hydropower Generation with Robotic Inspections
Penstocks are a vital component of hydropower generation by transporting water from the source to spin the turbine and activate the generator. As hydropower facilities continue to age, it is imperative that the essential equipment and vessels are routinely inspected and well maintained to avoid a lapse in power generation or environmental remediation. Robotic-enabled technologies, such as RUG, R-AUT, and RAW provide a full-coverage solution for holistic asset condition analysis to keep the water flowing for reliable power generation.
Did you know that U.S. dams were given a “D rating” in ASCE’s Report Card for America’s Infrastructure? Learn more about our infrastructure’s current conditions, and discover ways we can improve the rating for a safer, stronger, and more resilient future.