Hydrogen-induced cracking (HIC), a type of wet hydrogen sulfide (H2S) damage, is a condition commonly observed in the oil refining, petrochemical, chemical, and gas sectors.
If a certain level of hydrogen sulfide is detected in carbon steel, low-alloy, or other high-strength steels, it's deemed a sour service environment. This denotes its risk for wet H2S damage, including hydrogen blistering, stress-oriented hydrogen-induced cracking, and sulfide stress cracking.
Diving further into this topic in today’s post, we’ll cover some examples of assets that are susceptible to HIC, some real and specific examples of affected equipment, as well as some traditional and advanced HIC detection NDE/NDT methods.
First, as a brief refresher:
What is Wet H2S damage?
Hydrogen sulfide is a rotten egg-scented, colorless flammable gas that is dangerous to equipment when moisture—water—is present. Wet H2S conditions facilitate rapid corrosion and cracking, mainly from atomic hydrogen diffusing into the steel and collecting at defects.
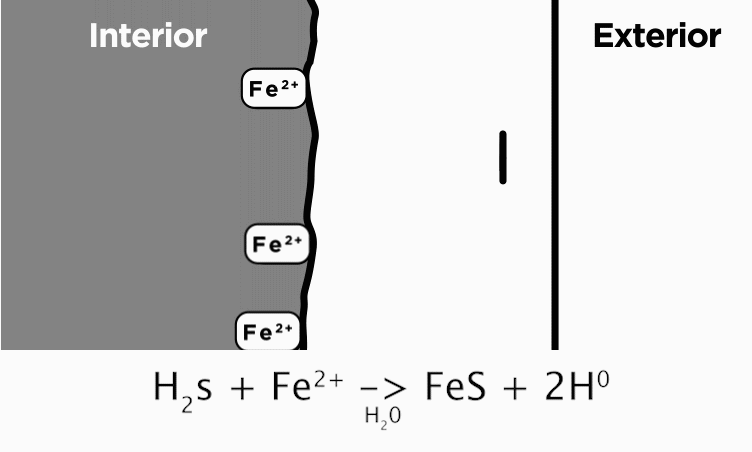
What is HIC?
According to Inspectioneering Journal, HIC is a common form of wet H2S cracking caused by the blistering of a metal due to a high concentration of hydrogen. The blistering damage tends to form parallel to the surface and to the direction of hoop stress. Blistering can sometimes be observed from the surface and often appear as tiny cracks. If gone undetected, HIC can lead to much more damaging forms of wet H2S damage.
Now, let’s take a look at some of the assets and equipment that are known to be affected by HIC.
At-Risk Assets
In oil and gas refining environments, as well as in petrochemical and chemical facilities, HIC is a risk to the safe and reliable operation of assets. Therefore, it is critical to recognize and monitor the equipment that might be affected by this condition.
In general, pressure vessels, pressure safety relief valves, and piping and tubing made from carbon and low alloy steels may be susceptible to hydrogen damage.
The American Petroleum Institute identifies the following situations and associated equipment to be monitored for wet H2S damage, including HIC.
- Hydroprocessing units: In these, according to the API, an ammonium bisulfide concentration of above 2% increases the potential for HIC and other conditions.
- Vapor recovery sections of fluid catalytic cracking (FCC) and delayed coking units: In these instances, cyanides significantly increase the probability of HIC and other hydrogen damage. Locations might include:
- fractionator overhead drums
- fractionation towers
- absorber and stripper towers
- compressor interstage separators and knockout drums
- heat exchangers
- condensers
- coolers
- Sour water stripping and amine regenerator overhead systems: Sour water or wastewater streams resulting from distillation, catalytic cracking, acid gas removal, etc., are sent through stripping systems, components of which include stripping columns, pumps, and tanks.
HIC and other types of hydrogen damage are relatively unpredictable, and thus, have been studied and documented for decades. As part of API Recommended Practice 941, Eighth Edition, the API shared data volunteered by its constituents for HIC-damaged equipment. The following are some interesting examples that demonstrate the unpredictable, ubiquitous nature of HIC.
- A section made of A106 piping: the damage was 27% of its thickness after 5,745 operating hours, while other pieces of the pipe in the same line were unaffected.
- Damage was concentrated in the overheated section of a hot bent steel elbow, while unbent straight portions were not damaged.
- In a series of 29 steel samples, 12 were damaged; 17 were not.
- The heat exchanger tubing in the tube sheet was damaged.
- Catalytic reformer combined feed piping welds and base metal
- Stainless steel cladding on 0.5Mo steel
- After 2 years of service, all parts of the carbon steel pipe, including weld and heat-affected zones (HAZs), were satisfactory. However, after 4 years of service, welds, and HAZs of A106 piping showed cracks.
- Hydrodesulfurization unit hydrogen preheat exchanger shell had hydrogen blisters, intergranular fissuring, and decarburization in the weld metal.
These examples demonstrate the importance of having regular, comprehensive inspections to catch isolated damage or fast developing damage. The use of on-stream NDE and/or NDT tools to inspect for this damage are good options to balance cost and site logistics. The following examples include both traditional and cutting-edge detection methods and technologies that have and are being used today, whether alone or in conjunction with one another.
Traditional and Advanced HIC Detection
Visual Inspections: Traditional visual inspections of pressure equipment are conducted by qualified individuals to identify any visible integrity issues and verify that the equipment can be operated for another fixed term. Although HIC can sometimes be observed, defect depth and severity cannot. With advanced hydrogen damage, relying on visual inspections is not sufficient in recognizing this condition.
Manual PAUT: A long-time solution has been periodic inspections using manual UT thickness gauges from the wall exterior to quantify loss or degradation and manual Phased Array UT to look for cracks within the walls. Operators typically have in-house capabilities, and the process can be inexpensive. The challenge, however, is that UT spot checking has negligible surface coverage, a very low probability of finding localized corrosion or damage, and can be time-consuming. As a result of these limitations, UT spot checks may not capture the worst damage and aren’t easily repeatable.
Magnetic Particle Inspection: A relatively simple technique, the process is an older NDT technique that offers both advantages and disadvantages. MPI requires magnetization of the component and subsequent coating with magnetic particles, which can be applied dry or in a wet suspension. In areas where metal is missing or the surface is disturbed—i.e., cracks—a magnetic flux leakage field is created. In other words, the current flow is interrupted, with cracks or defects attracting magnetic particles, making them visible. MPI is a classic NDT technique that is sensitive to surface crack detection, highly mobile, inexpensive, does not require extensive cleaning/surface preparationSince the surface is magnetized, this technique is limited to ferromagnetic materials and cracks must break the surface for the powder to take root. NOTE: After an inspection, the surface must be demagnetized.
Eddy Current: An efficient replacement of MPI, eddy current (ECT) uses electromagnetic induction of an eddy current probe or coil of conductive wire to produce its own magnetic field. As that magnetic field is exposed to the material surface, it induces an alternating current Any flaws will distort the current, thereby identified. While ECT offers advantages such as zero surface preparation, ability to detect very small cracks, speed, and cost-effectiveness, it is limited to conductive materials and is only effective for surface or near-surface defects.
For inspections that allow operators to test beyond near-surface level, UT methods offer distinct advantages over traditional NDT/NDE methods—beginning with automated ultrasonic testing (AUT).
Automated UT: With thousands of readings per square foot, AUT uses mechanical scanners to easily overcome the limitations of UT spot checking. With AUT, bulk data is gathered with a greatly increased quality of probability of detection. Continuous readings are achieved across the asset, rather than on specific, predefined points. AUT is an umbrella of many other technologies, including Phased Array Ultrasonic Testing (PAUT), which today is considered one of the most convenient and reliable nondestructive testing methods available.
By adding PAUT to rapid AUT, inspections can be performed at five times the speed and achieve up to 10 times the data compared to the same inspection being done with conventional AUT.
PAUT can be used alone or simultaneously with Time of Flight Diffraction (TOFD), on the same robotic platform. TOFD is an extremely sensitive tool that can detect cracking and flaws, regardless of orientation. Supplementing PAUT with TOFD offers many advantages for the detection of hydrogen damage such as HIC and SOHIC, and can be mounted on the same carriage in a single-pass way to take a deep look at the asset.
Capture the Entire Condition of an Asset
In conclusion, HIC-susceptible equipment should undergo periodic review to detect and quantify degradation or damage to ensure safe and reliable operations. The fickle nature of this damage mechanism warrants vigilance. While this has historically been achieved by visual inspections and surface NDE methods, modern AUT technologies offer many advantages—distinctly, the capability to non intrusively inspect the entire asset, find HIC damage beyond the surface/near-surface and obtain a data dense picture of the asset’s health.