Flight Deck
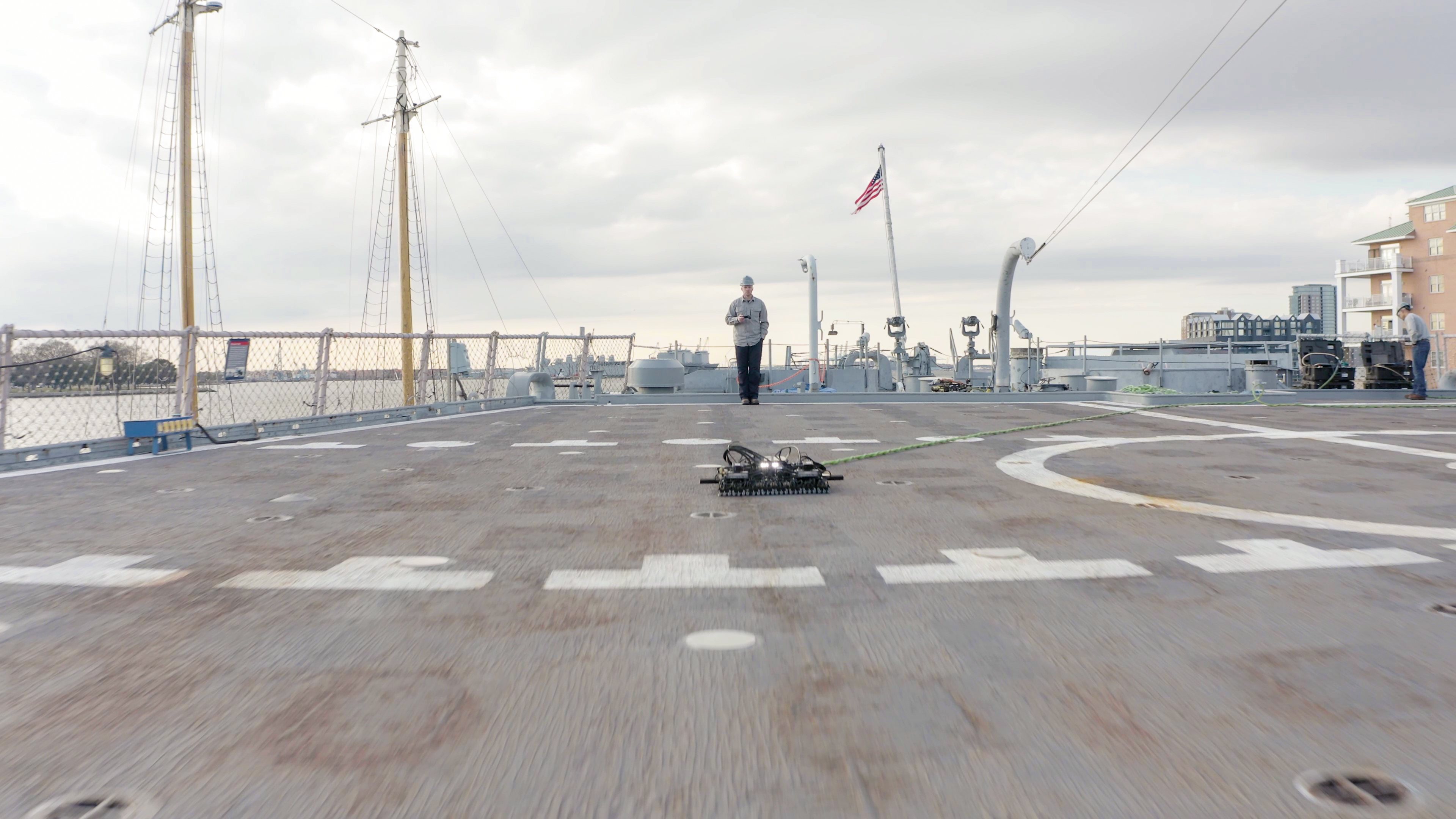
Challenge
- Ship availability is a major challenge for the U.S. Navy
- Vessels require continuous monitoring to maintain structural integrity and operational availability due to corrosive environments
- Traditional visual and manual inspections took more than two weeks to complete with 10 to 20 dedicated workers
- Manual inspections left pervasive gaps in coverage
- Once data was collected, it took inspectors two weeks to process and create a report
- Based on this report, it took 36 man-days to generate a repair plan
Solution
- Gecko's Cantilever process including:
- Data: Rapid Ultrasonic Gridding (RUG) inspection using TOKA® series robot
- Platform: Software modules presenting 2D & 3D corrosion maps and digital twin with color-coded thickness measurements, in-depth analysis, and robust reporting including repair recommendations
Result
- Inspection time reduced from two weeks to 12 hours
- Required labor and resources reduced from 10-20 workers to just one robot and two workers
- A total of 8 million UT data readings collected for a complete understanding of flight deck health
- Repair plan was generated in minutes, a process that used to take 36 man-days
- Targeted repairs were made which reduced maintenance time, costs, and resources
- The Navy’s workforce could be reallocated to mission-critical activities
- The destroyer’s maintenance cycle was completed on time, restoring the ship to fully operational status
Download the full case study