Flare Header Piping
Gecko Robotics helped a petroleum refinery reduce its upcoming turnaround scope and save over $1 million in asset replacement costs.
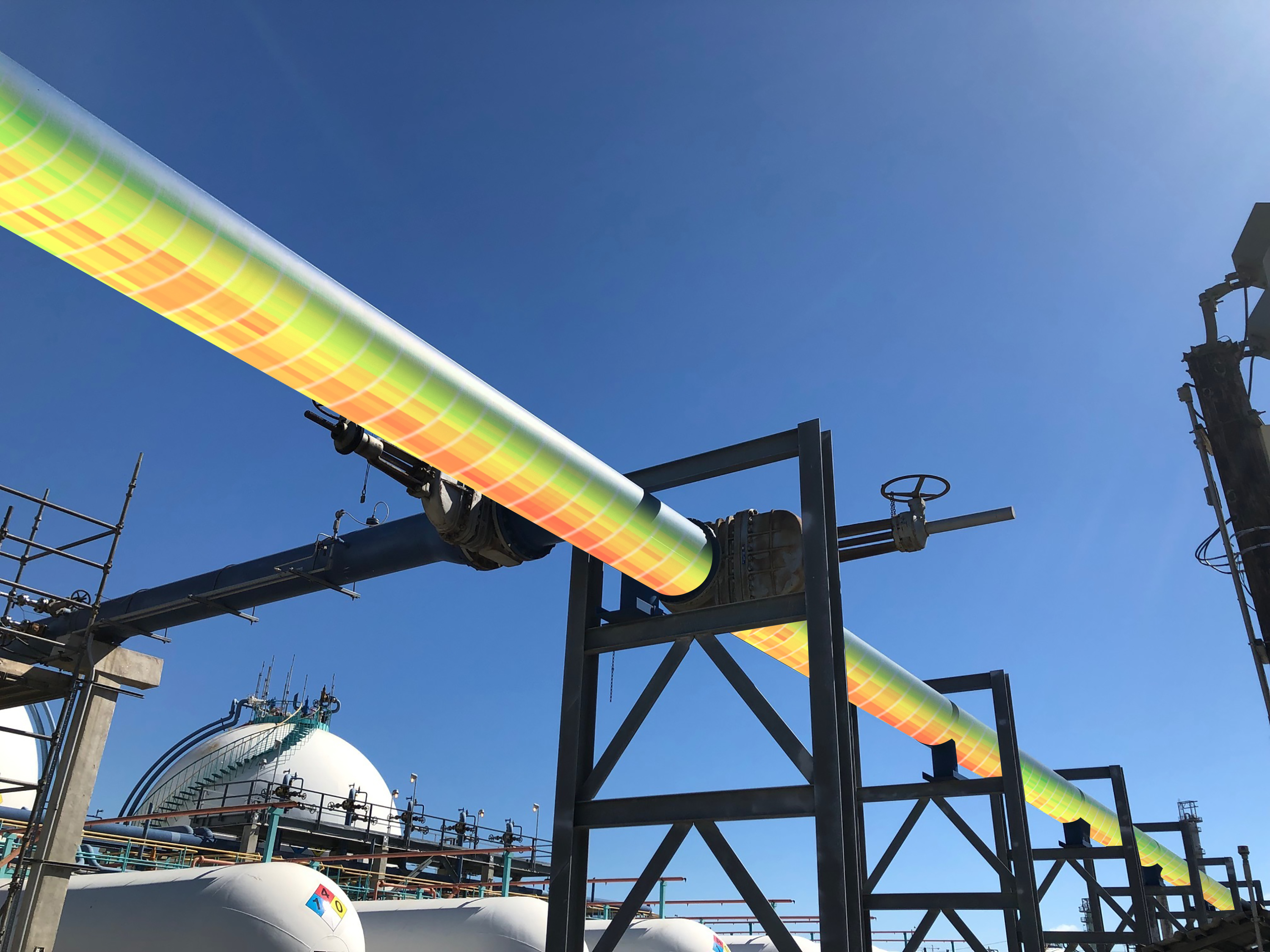
Challenges
- Based on previous inspection and service history, the refinery believed they would need to replace a 48” diameter flare line, estimated at $1.1 million
- Sought to reduce the scope of the upcoming turnaround by preordering materials and parts to stay on schedule
- Traditional inspection methods require assets to be taken offline, opened, and inspected during the turnaround
- Damage mechanisms found during an inspection can add time and costs, extending turnaround periods
Solutions
- RUG inspection using TOKA® robotic inspection platform
- Gecko Portal® Software for 2D & 3D corrosion maps with color-coded thickness measurements
Results
- In-service inspection of the flare line completed before the turnaround in five shifts without scaffolding or dedicated internal company resources
- Saved the refinery over a million dollars in replacement costs after confirming the flare line could safely operate for an additional 12 years
- 9.7 million UT data readings obtained
- Able to remove additional assets from the turnaround, inspecting 11 horizontal drums and two towers while online in just over two weeks