Chlorine Dioxide Storage Tank
Data-dense robotic inspection technology discovered pinhole-sized damage, avoiding potentially fatal outcomes at a kraft paper mill.
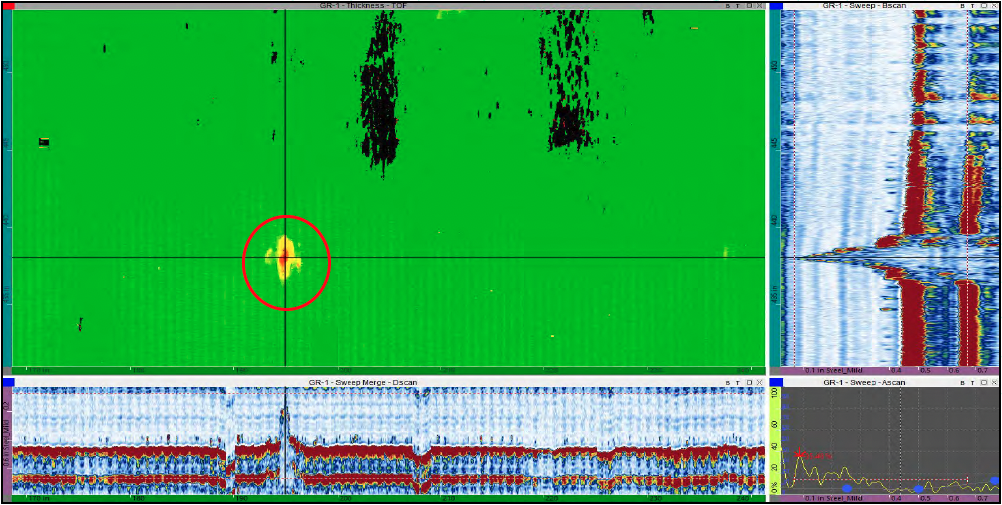
Challenges
- Chlorine dioxide (ClO2) is used for the paper bleaching process, but it is toxic to humans at ambient pressures and temperatures
- This vessel was located directly outside of a regularly manned control room
- ClO2 is highly acidic and will degrade carbon steel very quickly if exposed
- The storage tank was tile lined on the interior and insulated on the exterior
- Semi-annual visual inspection of the tile liner revealed no signs of liner failure or degradation
- Process Safety Management (PSM) audit determined the vessel needed to be stripped of insulation and inspected for corrosion under insulation (CUI)
- Previous inspection methods only covered corrosion monitoring locations (CML) or drop scans
Solutions
- Full-coverage external visual and ultrasonic testing (UT) inspection for CUI
- Robotic Rapid Automated Ultrasonic Testing (R-AUT) phased array corrosion mapping tool
- High definition S-scan data visualization and reporting to identify, locate, and size damage
Results
- Rapid AUT’s millimeter resolution found a small, isolated (1.75” or 44 mm diameter) corrosion cell on the inner diameter (ID) of the fourth shell course with a nearly 80% through-wall pit
- At the most severe location, Gecko Experts calculated a short term corrosion rate of 0.152” (4mm)/year, driving the removal of a 2’x2’ (61cm x 61cm) patch of shell and installed a flush patch and subsequent liner repairs
- Gecko Experts identified an additional 20 CMLs of ID corrosion with 20% wall loss or greater, signifying failure or damage to the tile liner
- Robot localization came within 1” (25mm) of the corrosion cells for all 21 CMLs
- Traditional A-scan, B-scan, or C-scan inspection methods and data visualization would have missed the insidious corrosion cell, potentially resulting in fatal outcomes
- The inspection found no CUI on the ClO2 storage tank but found significant manufacturing flaws